Micromechanics: Steel
We're getting our first taste of steel, while also learning one of classic watchmaking's most traditional skills: making a square from a circle.
The micromechanics program started with wood and moved us quickly to brass, but now we're working with steel, the hardest material of all—both literally and figuratively.
Even the softest steel is significantly harder than brass, which makes it more difficult to cut, but easier to cut to very precise dimensions. It requires different cutting tools for the lathe, and different techniques with our files.
For our first project, we're modifying the barrel arbor in our clock. The barrel arbor is the axle around which the mainspring winds, and we need to shorten it to fit into our clock design. This requires trimming back one end of the arbor, and re-filing the square portion that the modification eliminates.
Filing a square is one of micromechanics' principal skills. Squares are extremely common in watchmaking, and are usually found in the areas of highest torque—that is, the winding mechanisms and near the mainspring.
"Squares" in watchmaking don't actually have very sharp points. They tend to have rounded vertices, since the square is slightly oversized for the cylinder that it's cut from, and there's a formula for forming them.
Watchmakers must be able to file a perfect square, and the lathe helps you, but doesn't do all the work. Our lathes have indexes which allow us to rotate the workpiece 30° at a time, and the roller rest allows the file to keep a steady height as we work. Still, the file must run across the workpiece at perfect right angles, and that's up to the watchmaker to pull off.
The stakes for this project are high. We don't have spare parts, so if we make a mistake, we have to form an entire barrel arbor from scratch. Luckily, I was able to keep all of my cuts within tolerance, and the project can move on.
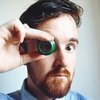
Watchmaking student at the Lititz Watch Technicum, formerly a radio and TV newswriter in Chicago.