Real Life Repair: Universal Geneve Polerouter
This is a really cool watch, and I'm really excited to have the opportunity to work on it.
The Universal Geneve is a brand that is rocketing up in price on the vintage market, and the Polerouter is one of their most-coveted models (behind Valjoux-based chronographs). It originally debuted in the 1950s to celebrate Scandanavian Airlines Systems' polar flights from the USA to Europe, and was penned by a young Gérald Genta, long before he was a legendary watch designer.
Even without those positives, the Polerouter is an interesting watch because most of them utilize a "microrotor" automatic system. Most automatic systems sit above the movement, adding height. Traditional automatics are more cost-effective to build and more mechanically efficient because of the rotors' greater leverage, but the microrotor had a brief time in the limelight when thin was in, mostly during the 1960s and 1970s. This watch uses a calibre 69, a '60s adaptation of the company's earlier cal. 215 and 218.
The automatic module is completely modular, which helps with assembly and timing. Primary timing adjustments are usually done at the "base movement" level—that is, with just the timekeeping elements installed, not the automatic, date or any other complications.
All of this movement's quirks are related in some way to the microrotor system. While it saves height, the placement of the automatic in the same plane as the geartrain causes space and layout issues. It also requires tiny parts, including this ridiculously thin click spring, which is mercifully bonded to the click itself.
The lack of space not only relocates the reverser atop the barrel, it's also dramatically upsized! The greater wheel diameter lowers the torque required to wind the barrel, though it means that the rotor must make more rotations to wind the spring. This orientation isn't unique to Universal by any means, but it is unusual.
Much weirder is the bizarre way that the movement drives its hands. Because the geartrain must contort itself around the automatic, a traditional center wheel is impossible. Instead, Universal uses a split intermediate driving wheel, exactly like the 3rd wheel on my Vostok! The split wheel allows the barrel to take out the backlash in the tooth mesh, keeping the minute pinion from wobbling around.
Then, atop the minute pinion, a traditional friction spring lifts the seconds pinion to take out the seconds hand's backlash. That makes two complementary anti-backlash systems, sitting in immediate proximity, but not interacting with each other. The friction spring fits below the 3rd wheel, which means that the spring is constantly pushing the 3rd wheel (and by extension 4th and escape wheels) to the side during assembly. This was one of the trickiest and most annoying train bridge installations that I've yet encountered, for that reason alone.
The great wheel and 3rd wheel had pretty significant scoring (normal in an old watch in high torque areas like this), which I burnished out.
Otherwise, the movement was impressively free of watchmaker damage, and runs well! Universal made nice watches, and they're a pleasure to service—especially when they're in good shape to begin with! As with many vintage watches, parts can be tricky and expensive to find. Aside from a new mainspring (which should be installed on all vintage timepieces) and burnishing those two pivots, this watch didn't need anything replaced.
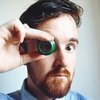
Watchmaking student at the Lititz Watch Technicum, formerly a radio and TV newswriter in Chicago.