Ébauche Assembly & Finishing

Our first post-SAWTA assignment is an exciting peek into the world of high-end watchmaking.
We have been supplied with a raw ébauche, which we are to assemble and decorate. An ébauche is a fully machined, but completely raw movement. Our task is to make it into a high-grade timepiece without damaging anything.
Unless a watch's bridges are completely handmade, like our school watch, this is roughly the stage at which most watch manufactures will begin work after machining. These are straight out the CNC machine, and need a watchmaker's touch.
The first step in assembling the watch is to locate the bridges by fitting steady pins into the mainplate.
Once the bridges are in place, the jewels and all other components can be fitted to test functionality. Here you can see the raw machine finish on many of the components—since this is a finely-made ébauche, it won't be hard to remove. But it must be removed.
The first step in decoration is anglage and satinage. Anglage involves the bevels, while satinage is simply replacing the machine finish on the sides of the bridges with a line finish.
Long-time readers will recognize these steps from the school watch project, the second half of which was finishing intensive. I talked at length about beveling, and again about polishing those bevels. This time, after hand-lapping and burnishing the bevels, I used a slightly different approach.
While I previously used a felt wheel and a rotary tool to polish my test bevels, this time I used pegwood in the lathe with extremely-fine polishing compound. The wood is significantly harder than the felt, which keeps the bevels flatter, while the shape of the pegwood makes it much easier to control. It took some work, but the bevels are completely polished without a trace of scratching, even under high magnification.
Is this a bit of a cheat? Yes and no. The traditional way to polish bevels is by hand, with pegwood and diamantine powder. Modern manufactures often use wooden wheels with polishing compound for production hand-finished watches, presumably for reasons of efficiency. The wood works wonderfully, and I wanted to try this idea for reasons of time and curiosity.
I'm quite satisfied with the results.
After the sides and bevels of the bridges are finished, it's time for perlage on the mainplate (as well as the recesses on the barrel bridge and balance cock) and côtes de Genve on the tops of the bridges.
The striping helps highlight the bevels by providing a distinct grained finish on either side of the polished surface.
With the decorated plate and bridges reunited, it's starting to look like a real watch!
The bridges and mainplate will now be sent out for electroplating. Meanwhile, I have plans to make a few modifications under the hood for an even more personal and aesthetically pleasing result.
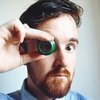
Watchmaking student at the Lititz Watch Technicum, formerly a radio and TV newswriter in Chicago.