Micromechanics: Watch Components
After learning the ropes on bigger things, we're making our first watch parts.
Everything we've made in micromechanics so far has been either a tool or a clock part. Those are nice and large, with comfortable tolerances for newbies. Now we're starting to fabricate watch components, though still "big" ones.
We're starting with parts for the 6497 for many of the same reasons that we used it to learn watch service—the movement is generously sized, making makes things easier. A bonus is that our school watch is based on the 6497, so we can use these parts when we build that project later this year.
Our first component is the yoke, which is part of the dial side components on a watch. These parts generally relate to the winding, setting and date/complication functions of a watch, and are often overlooked by the consumer for the simple fact that they're buried beneath the dial. That said, the yoke is a critical component that would render a watch useless if poorly manufactured.
The yoke is a lever which allows you to wind the watch or set the hands by pulling the crown in and out. The *click click* of the stem when you pull it is caused by multiple components, including the yoke, which pushes the sliding pinion back and forth, engaging the crown wheel (to wind), the intermediate setting wheels (to set the hands) and the date quick adjusters (where applicable).
Yokes generally look a bit like a boot, and the geometry of its various curves and angles are very precise. The sole of the "boot" is an inclined plane that pushes the set lever back and forth, and the "calf" must sit snugly in the sliding pinion's slot with minimal play to avoid slop.
In the photo above, the Swiss ETA yoke is on the left and mine is on the right. With about 8 hours of work invested, my piece actually exceeds the finish level of the factory part (which is admittedly a low-grade one). Hand work tends to be superior to machine craft in most cases, and this is no exception. To the untrained eye, the higher "polish" of my piece might be the biggest differentiator, but the true sign of craftsmanship is in the crisp edges, especially at the point where the curved base meets a flat—filing that corner is a whole proficiency of its own!
Forming the yoke was straightforward. After shaving down the steel on a shellac chuck, I simply shellacked the factory yoke on the metal and used it as a guide to saw and file the steel to completion. That makes it sound easier than it was—shellac is very brittle, and tends to separate when too roughly clamped in a vise—but having a good working piece as a guide makes the process simple. In the future we may not have such luxuries, especially when working on worn-out vintage components.
Because this is a working component, it has to be heat treated for hardness and brought to a near-polished state to reduce friction with other components. The broad surfaces have been lapped down to a 5 μm grit film, while any friction surfaces have been taken to a pre-polish with 3 μm lapping film.
It's incredibly satisfying to make a watch component, install it in a movement and have it work! We'll be doing even more parts soon.
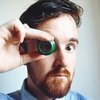
Watchmaking student at the Lititz Watch Technicum, formerly a radio and TV newswriter in Chicago.