Micromechanics: Heat Treatment
Steel is harder than brass, but the hardness of steel varies widely depending on how it's been produced and treated.
The steel that we use to make objects in micromechanics is a high-carbon oil steel, which we'll need to heat-treat for proper wear resistance.
Heating up steel causes dramatic changes in the metal. Steel, in its most basic form, is just iron and carbon, usually between 0.3%-2.5%. Heating the metal to over 1,400°F (and quickly cooling it) alters its crystalline structure, increasing its hardness and brittleness dramatically. In fact, it becomes so hard and brittle, that it's essentially unusable—it's like glass. That's where tempering comes in.
Tempering is a similar process to hardening, but it's slower and cooler. The hardened piece is heated over a plate of brass shavings to about 600°F, at which point it's turned blue. Tempering reduces the hardness, but more importantly it also dramatically reduces the brittleness to a point where the metal can be used as a clock or watch component.
Tempering color phases of steel (Wikipedia).
Tools are only tempered to about 425°, when the steel is the color of straw. This is a harder and more brittle phase, and since a cutting tool must be harder than its workpiece, it will be able to machine blued steel, which is softer.
All of our heat treatment is done by hand, with a MAPP gas torch, binding wire, pliers, brass shavings and a jug of water. Manufacturers use pyrometers to make sure that the temperatures are precise, but we're able to use our eyes since the color phases of steel are easily seen and reproducible. Glowing a bright orange-yellow means the steel is around 1,400°, while the aforementioned blue sheen means that it's 600°. Despite the seeming imprecision of eyeballing it, it's effective!
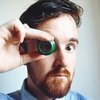
Watchmaking student at the Lititz Watch Technicum, formerly a radio and TV newswriter in Chicago.