Micromechanics: Toolmaking
Sometimes the only solution to a problem is something you have to make yourself.
The hour hand on our school clock is riveted to its hub, but we don't have any punch in our staking set even close to the size required to do the job... So I made one myself.
The punch here is actually machined to be precisely held in a stake from our staking set, the better to keep things perpendicular when we hit it with a hammer. However, that means that it has to be carefully heat-treated.
Since the working end of this punch will be slamming into metal and deforming it, the steel must be hardened and tempered. Since it's a tool, it should be tempered to straw, and that's the color you can see in the photo. At the same time, a hardened "tail" (the bit inside the stake that holds it in place) would be too brittle, so that must stay untreated. The solution is to heat-sink the handle while torching the other end.
Making a punch like this is a fairly simple affair (it probably took an hour to 90 minutes, including heat treatment), but it's a good bit of experience for the real world. At school we have a wonderful selection of tools to use for whatever we need, but out in the field, we'll be much more restricted. Making a tool by hand is an economical and satisfying way to solve this puzzle.
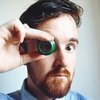
Watchmaking student at the Lititz Watch Technicum, formerly a radio and TV newswriter in Chicago.