Micromechanics: Boring
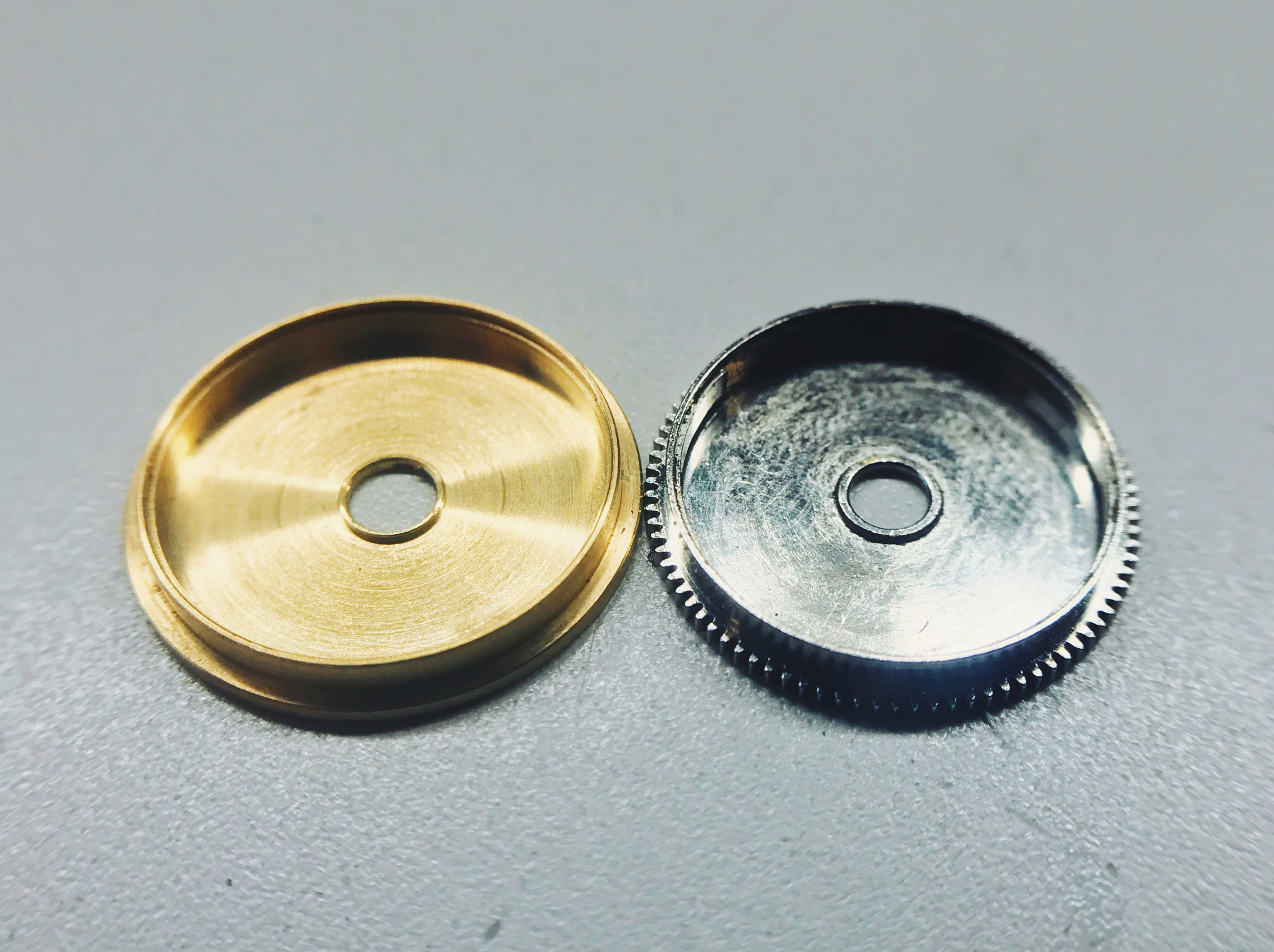
We've learned to do many things with our lathe, but they've all been machining operations on the outside of a workpiece. Now we're beginning to go inside.
Boring is the most precise way to make a hole, full stop. Drilling has inherent variability built in (drill bits can shake or wander), and broaching can give holes a funny shape if you aren't careful. Boring can form perfectly cylindrical holes to a precise diameter, and they're the only way to do some kinds of holes (which we'll tackle later on). The only problem is that it's considerably more time consuming.
Boring requires an entirely new cutter shape, as well as a new cutter configuration. While in traditional lathe turning the cutter is (roughly) perpendicular to the workpiece, boring places the cutter on about the same axis.
Boring also requires you to work blind, and to trust the lathe as a measuring device. Since you can't directly measure the size of holes with our calipers, you have to be extremely careful and accurate with your boring to achieve the correct size of holes.
For practice, I've formed the barrel of our 6497. The barrel holds the mainspring, and forms the first link in the watch's powertrain. It's a tricky object to machine—the outside surface has two planes (one for the barrel wall and one for the teeth, which aren't cut yet), and the inside has the lip for the lid, the barrel wall, the floor and the shelf for the barrel arbor to rest upon.
All of these must be machined within very small tolerances. Just a hundredth of a millimeter or two, and the lid will either fail to snap in or will simply fall out. A hundredth or more on the arbor shelf, and you're out of endshake, causing the arbor to bind during winding.
This tiny piece of brass is just a few millimeters deep and barely a dozen across, but it took a whole 8 hours to machine. Luckily, it works!
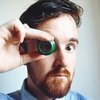
Watchmaking student at the Lititz Watch Technicum, formerly a radio and TV newswriter in Chicago.