Real Life Repair: Jewel Grinding
Jewels are commercially available in a wide range of sizes, but sometimes you have to custom-grind one to fit an obscure need.
Among the modifications that the Soviets made to the Zenith 135 to create the Vostok 2809 were the addition of cap jewels on the 3rd and 4th wheels. Capped wheels tend to run with reduced friction (being supported on the very tips of their pivots), but only if they're made properly. These weren't.
Proper capped wheels require conical pivots and "olive" hole jewels to reduce friction points as much as possible. Vostok chose instead to use regular square pivots, which mostly negate the friction-reducing benefits of the capped jewel system. They also used strange, non-standard hole jewels.
Since one of those weirdly-sized hole jewels was broken, I had to grind a new one to fit. This required taking a normal bridge jewel and grinding a dome onto the flat bottom. Luckily, since the pivots are square, I didn't have to modify the geometry of the hole jewel at all—thanks, Vostok!
Jewels are made of synthetic ruby, which requires diamond to cut and shape it. But even before that, the jewel must be mounted on a mandrel in the lathe. Here's a 0.18 mm "pivot" I hand-cut with a graver to center the jewel onto the mandrel, next to a 1.00 mm screwdriver for scale.
Once glued, diamond paste is applied to a brass lap and held against the jewel to form the dome. Diamond paste is very non-aggressive, so it's time-consuming, and the jewel must be polished at the end of the process with a very fine grit paste, which takes even longer.
The dome on this jewel is partly aesthetic, but it also helps center the oil. The high part of the dome sits closest to the flat cap jewel, and capillary attraction will hold it there around the pivot instead of wicking it away to the sides.
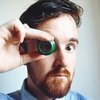
Watchmaking student at the Lititz Watch Technicum, formerly a radio and TV newswriter in Chicago.