Moonshot Project: Bi-Metallic Balance Wheels
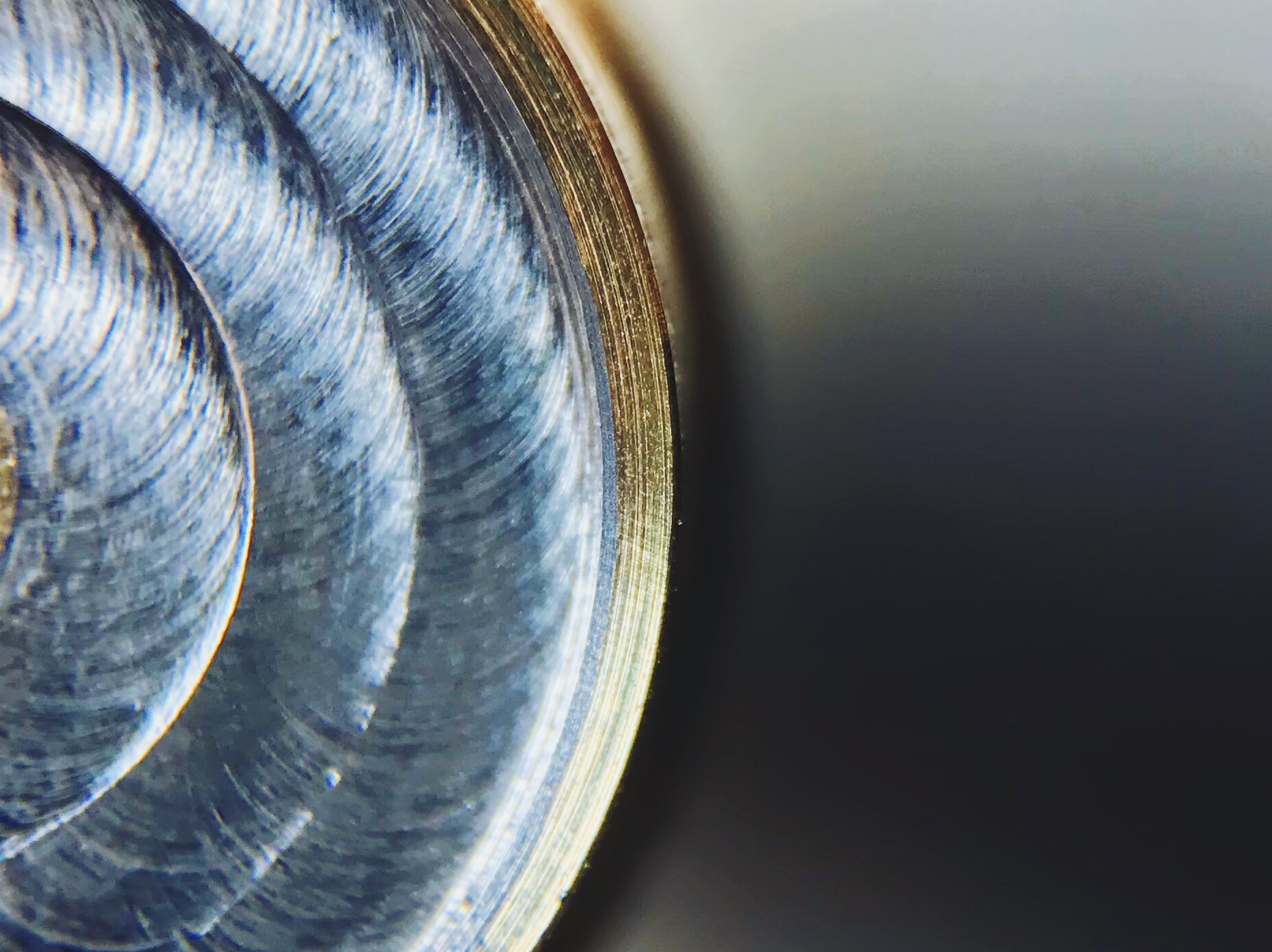
Justin and I are embarking on a wild journey into horological history. We're attempting to create our own temperature-compensating, bimetallic split balance wheels, using only traditional tools and methods.
One of our principal goals for this project is to determine a reasonable and reproducible process by which watchmakers can make their own bimetallic balance wheels. This information isn't intended to be proprietary, but it is experimental. I can't promise that this will work, but I can promise that we will share every bit of knowledge that we learn along the way, in the hopes that someone might find it useful.
The bimetallic balance was once the absolute pinnacle of precision horological technology, and reigned supreme for centuries... Until it was made instantly obsolete by modern metallurgy, and lost to the dustbin of history. That was nearly 100 years ago.
Heat and cold make metals expand and contract, and cause springs to lose and gain strength. Early balances were made of a single metal, which would grow in diameter with heat, while their steel hairsprings would get weaker (and visa versa). The combined effects of these changes caused watches to lose several minutes per day when subjected to changing temperatures.
Bimetallic split balances were invented to solve this problem of temperature. They're made of two metals with different coefficients of thermal expansion (brass and steel) which are thermally fused, and the rim is cut in two places so the rim can expand and contract as "arms" instead of as a single unit. Together with careful placement of timing screws, the motion of the balance arms was carefully controlled to counteract any changes in the hairspring's strength, vastly improving timing results.
The first step in this project, and the one that has frustrated all students who have attempted it in the past, is thermally fusing the brass and steel together. Since bimetallic balances have been outdated for almost a century, there is precious little literature to guide us through this process. The books that do exist just skip over the "how" entirely, and simply say to fuse the metals. Okay.
Brass and steel have vastly different melting points, but the steel's is more critical, since it forms the foundation of the wheel. We're using O-1 tool steel, which has a brazing temperature of around 2150°F. Our kiln only goes to 2000°F, and then only briefly, so we decided to use a small oxyacetylene jeweler's torch to do the job.
It worked.
More details coming up soon!
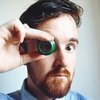
Watchmaking student at the Lititz Watch Technicum, formerly a radio and TV newswriter in Chicago.