Real Life Repair: Screw Polishing
Marred screws are the hallmark of a sloppy watchmaker. Many watches have lived hard lives, and have scratched and/or rusty screws to show for it. Refinishing screws is a delicate process, but it can truly make a difference in a watch's appearance.
We made a screw polishing tool last year as a micromechanics exam, and it's actually a quite simple mechanism that looks a bit like a fish. The two "fins" have adjustable height screws and the "body" has screws pointing inward that clamp on a pin vise. Together with the screw (held in the pin vise) and the height screws, the entire contraption forms a tripod that can be finely adjusted to hold the screw head flat against the lapping plate and polishing block.
Getting the head perfectly flat is the hardest part of screw refinishing, but it's also the most important. Any deviation from the original flat surface will quickly form a facet, and that will eventually make the entire screw head uneven. We use a mirror to ensure that the entire surface of the screw is in contact before taking it to any abrasives.
Once set up, the screw needs to be ground on ever-finer grades of lapping film until all deep scratches and gouges are gone. With vintage pieces, being conservative is the name of the game, so I usually start with pre-polishing film—it takes longer, but I remove as little material as possible.
After the scratches are gone and only the faintest swirls remain, the screw is polished using ultra fine diamond paste (50,000 mesh, or so) on a zinc or nickel lap.
Watch components are considered truly "polished" when no scratches are visible at low (3x) magnification. This is an extremely time-intensive process, and is usually only done to high-value vintage restorations, but these screws belong to my Soviet chronometer clone. At this point, they look nicer than they did when they left the factory!
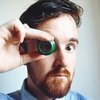
Watchmaking student at the Lititz Watch Technicum, formerly a radio and TV newswriter in Chicago.